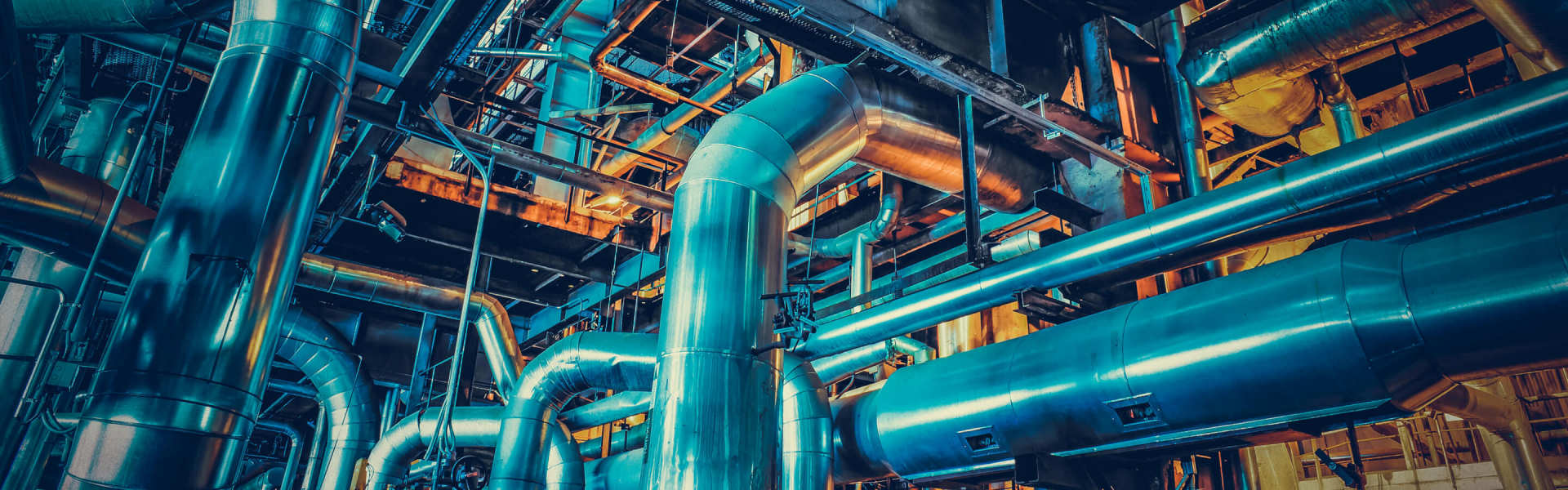
Component or Cartridge
How to Choose the Right Seal
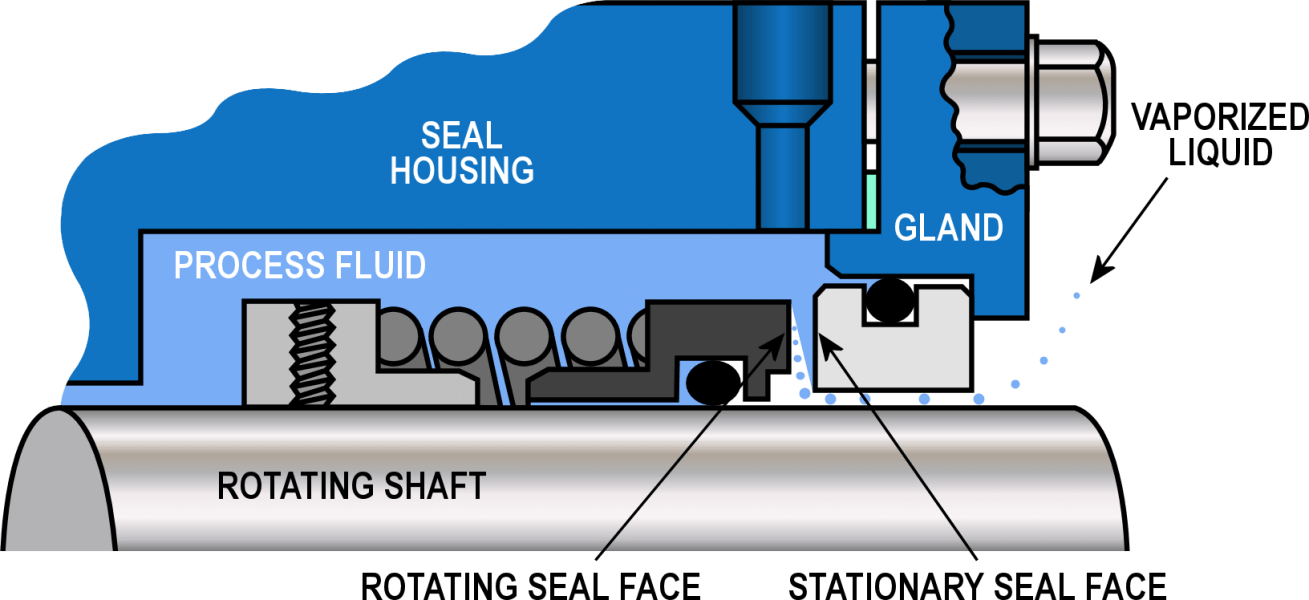
Mechanical seals in pumps prevent fluid leakage between a rotating shaft and stationary housing. Each seal consists of a rotating and stationary element with precision-smooth, lapped mating faces. Seal performance depends primarily on the condition of these faces and the applied pressure. Other critical factors include heat, vibration, and fluid characteristics. Depending on the specific application and user needs, different seal types may be appropriate.
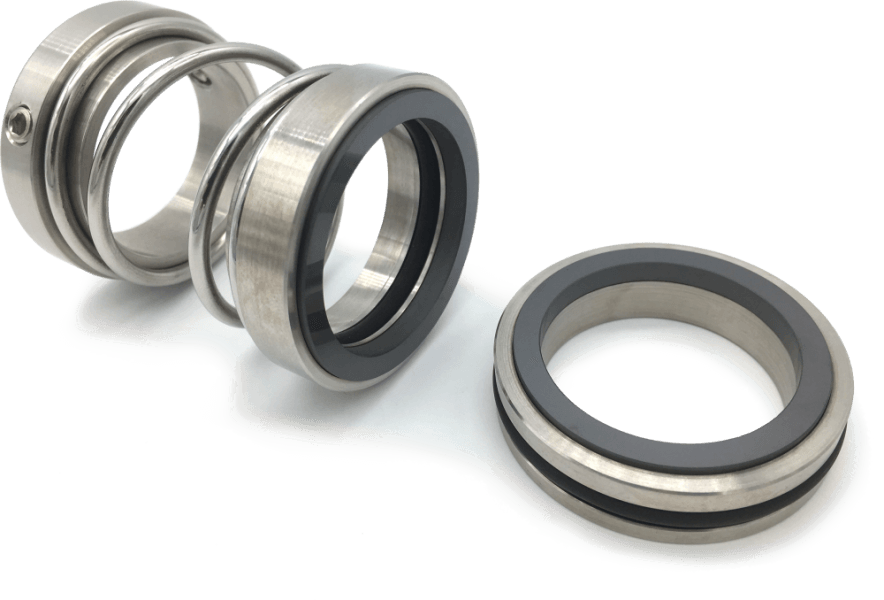
Component Seals
Smaller pumps commonly use cost-effective component seals, which perform well across many applications. However, these seals must be installed piece-by-piece, requiring special handling and careful attention from technicians. Improper manual adjustment of the spring tension can lead to leaks, necessitating disassembly of the pump.
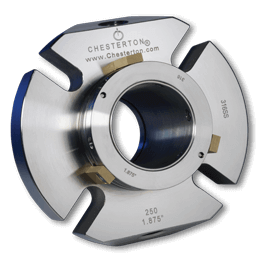
Cartridge Seals
Larger pump designs, such as ANSI process, vertical turbine, and split case pumps, offer the flexibility of using cartridge seals. While cartridge seals typically cost more than component seals, the long-term benefits may justify the higher price. Cartridge mechanical seals and component seals use similar components, but the stationary parts are preassembled in a housing, and the rotating parts are preassembled on a shaft-mounted sleeve sealed with an O-ring. Cartridge seals have preset spring tension, and a retaining device holds the rotating and stationary elements aligned until the seal is mounted.
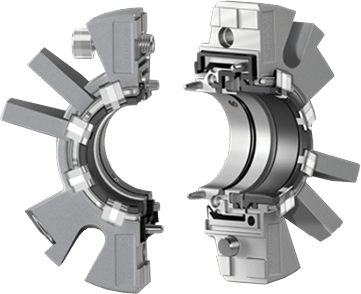
Component vs. Cartridge
Cartridge mechanical seals typically cost two to three times more than component seals upfront. However, the higher initial investment can be offset by the long-term cost-effectiveness of a cartridge seal. The advantages of using a cartridge seal over a component seal are as follows:
- Ease of Installation - Cartridge seals are easier to install since all components come preassembled. However, if a technician fails to set the proper spring tension in the seal, the pump may leak, and the seal could become permanently damaged. Cartridge seals include a retaining device that keeps the rotating and stationary elements aligned until the seal is installed. While an experienced pump technician may not consider this a significant advantage during a planned overhaul, it can be extremely beneficial during an emergency shutdown.
- Split Seal Designs - The split-design of cartridge seals allows for easy seal replacement, requiring minimal disassembly of the pump and/or motor. This can significantly reduce downtime during emergency outages. Split seals are an excellent choice for split case and larger vertical turbine pumps.
- Impeller Adjustment - Pumps with semi-open impellers often require periodic adjustment of the impeller face clearance. Users can make this adjustment by moving the pump shaft axially, which can alter the seal tension. Resetting the seal tension on a component seal typically requires extensive disassembly of the pump. In contrast, most cartridge mechanical seals have retaining devices that can be easily reinstalled to realign the stationary and rotating elements, simplifying the process of resetting the seal tension after adjusting the impeller face clearance.
Making the Right Choice
For a cost-effective, long-term pump maintenance solution that accommodates in-service seal replacement, a cartridge mechanical seal is likely the best choice. This type of seal also enables the conversion from a packing seal to a mechanical seal. However, when low initial cost is the priority, component seals paired with a skilled pump technician may be the optimal option.